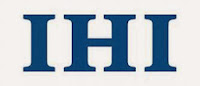
I. Simulation
There are simulations for discrete events such as physical processes but computer simulation can also simulate real-world phenomena such as the spread of information and even “change” behavior and how it affects an organization.
This workshop focused on how to take national research based metrics such as the rate of change readiness, adoption, and adaptability for organizations (among other metrics) to create a simulation to help the user determine the most effective strategies for implementing programs such as readmissions.
The workshop facilitators also spend a good amount of time speaking to the validity of data that is used as input for these models and techniques to arrive at conclusions with some reliability using Fermi decomposition techniques, which is an estimation technique. You can then PDCA the simulation model as you learn more about how your particular organization behaves.
II. Run Charts vs. Red, Green, Yellow
Many organizations use Red, Yellow, and Green to indicate the status of measures. This style of displaying metrics is limiting and can cause confusion. This can stifle crucial conversations and lead leaders to the wrong conclusions.
Instead, the presenters argued, using simple control charts can illustrate interdependencies of processes; prove that your processes are out of control (despite being within control limits), and allow leaders to draw valid conclusions. This is something that the classic Red, Yellow, and Green dashboards cannot convey well.
To show the difference, a handout exercise was performed during the workshop where the same metrics were presented, both in standard dashboard style with the use of color coding (Red, Yellow, and Green) and then again using Shewhart charts (control charts with upper and lower bound limits).
The presenters covered the 5 rules for detecting special cause in your processes using control charts, which are:
![]() |
Example Control Chart |
2. A run of eight or more points in a row above or below
the mean
3. Six consecutive points increasing or decreasing
4. Two out of three consecutive points near a control limit
5. Fifteen consecutive points close to the mean
III. Real-time location systems (RTLS)
The presenters described RTLS as: Wireless technology that permits the tracking of moveable medical equipment, patients, and staff.
There are many reasons why an organization may want to use this technology including: Easily tracking of equipment that may be recalled, reduced excess purchasing, address shortages enterprise wide, better equipment planning, temperature monitoring on sensitive equipment.
Another application, not mentioned in this workshop was the ability to move to a real-time simulation forecasting model. If a system has the ability to input data into the model immediately (or close to), then a department or hospital may be able to forecast problems, days in advance (much like weather forecasting).
Think you need help? Please contact me at Astrozuggs@gmail.com with any questions you may have about this or any other Continuous Improvement Question.
Also, please see my other Continuousimprovementpal blogs